In 1492, a Spanish-based transatlantic maritime expedition led by Italian explorer Christopher Columbus encountered the Americas, continents which were virtually unknown in Europe, Asia, and Africa and were outside the Old World political and economic system. The four voyages of Columbus led to ongoing European contact with the Americas.
The aim of the expedition was trying to find a new route to go to Asia (there have been some thoughts against that theory). We can infer that, at least, there was an objective behind: to discover new things. Things such as new routes, lands, goods, people (maybe?), … Despite that, they were expecting to come back with the information.
Whether you are a fan of history or not, you may still find similarities between the discovery of the Americas and the development in the modern industry of today.
Industrial context
On the shop floor of a factory, you find a lot of machines carrying out a lot of important tasks. All of them. Maybe working together, as part of sequential activities in a chain, or acting as a single entity, so-called, functional island. This is the tangible part of the industrial context, where being in front of the machine and having a look at it we know whether the machine is running as expected or not. The more time working with the machine the more knowledge we can have.
Does it mean we have to be in front of the machine or process to know if it is running properly all the time? When realizing there is an issue, is there someone we can call to come to the machine to see what’s the issue?
We can ask ourselves:
How many Christopher Columbuses are present in our factory? We do not need more.
How many times should we discover the Americas? Meaning, going to someplace to get information or clear understanding about a specific issue or just asking if the machine is running properly.
Connecting the islands
One of LEAN principles is motion, meaning: wasted time and effort related to unnecessary movements by people by getting information or having a clear view of what is happening. And this is translated into indirect times growing the non-added value activities.
There is a huge potential of connecting the functional islands in a digital world. It is mandatory to have a clear vision of what is happening, when and why at any time and at any place of the factory; and, of course, without the need to move anywhere.
Any machine must be connected to a central location to be able to gain the most relevant information. Only in this way, it will be possible to manage it without being in front of it.
Perhaps the machine or process has an HMI where the operator can operate it and see what the behavior of it is. Depending on the business and how the machine needs to run, you do not need to replicate the same functionality in a central location, but just exchanging the information that will be necessary for other purposes.
Purposes of integration
As said, on the one hand, it is important to reduce indirect times or overhead costs.
But, on the other hand, and depending on to whom we are addressing the question, the answer might be different. The following table might describe some of the interests that any department or area may have:

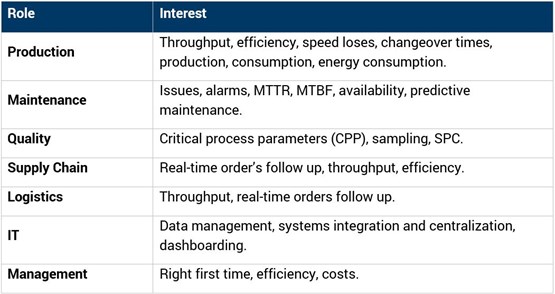
In the end, it necessary to improve the business and activities around it, and getting insights from what the process is telling us.
No more expeditions as explorers
In conclusion, and coming back to the main topic, what is necessary is to prevent anyone from being explorers, trying to discover new “Americas” at the shop floor, but being proactive about our processes.
Seeing people running around the shop floor without any specific direction is a clear indicator that something is not going in the right direction if we want to optimize the P&L of our business.
Author
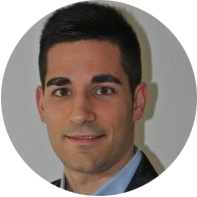
Oriol Llargués
Manager
ola@frontmatec.com
+34675820857